KEN ZUPAN
University Design Lecturer: Industrial Designer

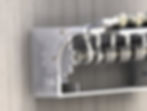
Above: Rendering of the final mechanism using SolidWorks. Individual parts of this assembly were exported as .STL files to be 3D printed later on.
Above: Foam sketch model to demonstrate proof of concept of the mechanism. Students have modeled the crank, cams and lifters using simple materials.

Above: The final product constructed of laser-cut acrylic, wood and 3D printed ABS. To maintain its kinetic nature, the clock is:
1. Manually activated using a natural turning on and off motion with a rotational sensor.
2. Each passage of time segment is indicated using a dropping bird using the force of gravity.
3. In addition to the dropping bird, the progress of time is indicated with an LED which dims as each bird drops.In terms of interaction, the birds individually drop to indicate the passage of time.
https://iat336wyc14.wordpress.com/
Task: For this project in my IAT 336 course, my students were comissioned to create a functional timepiece that would be embody the qualities of a kinetic sculpture. In other words, how could the concept of time be displayed utilizing natural, physical phenomena e.g. gravity in a mechanical assembly to indicate the passing of time.
'Drops of Time' is a kinetic artifact which attempts to integrate natural cues to display time passage. It is influenced by Song Su's water clock design (c. 1088 AD). A marvel of engineering for its time, the clock was entirely driven by water which drove mechanical gears and linkages inside. In this context, the theme is that of a timer, using six dropping birds which activate at (1 hour) timer or 30 minutes (each bird represents 10 minutes or 5 minutes).
Teaching Focus: The object of this exercise was for students to build upon skills learned in IAT 106 (spatial thinking) course. In this course, students built a kinetic sculpture or automata of an animated figure driven by a single crank and gears. In this exercise, the threshold of complexity and sophistication was raised higher. First, rather than use found objects such as wire hangers and cardboard, the students were required to use 3D printing (ABS) and laser cut acrylic. These fabrication processes and materials allowed for much higher precision in the mechanism and smoother movements.
As a result of the compexity of many of the concepts, my students relied heavily on low-fidelity sketch models to test out their mechanism designs before committing to their final designs. As is seen at left, the team designing 'Drops of Time' created a test assembly using wood dowels, foam core and pink foam to model the crank, cams and lifters. This proved to be an invaluable iteration as shape of the eccentric cams required refining. Something that could not be done using a sketch.
"Upon further analysis, we question ourselves: 'what if the weight is too heavy, how will we ensure the board stays in balance throughout the duration of the timepiece movement? We came up with a solution via the creation of a follower support".